Special Boeing 747s
- 747 ASB (Advanced Short Body)
- 747 CMCA - Cruise Missile Carrier Aircraft
- 747 Large Cargo Freighter (LCF) Dreamlifter
- Boeing 747 AAC (Airborne Aircraft Carrier)
- Boeing C-33
- Boeing E-4 Advanced Airborne Command Post
- Boeing KC-33A
- Boeing VC25 Air Force One
- Evergreen Supertanker
- Shuttle Carrier Aircraft
Boeing and the United States military have adapted some variants of the 747 into transport aircraft and platforms for scientific experiments. A summary of all the aircraft is outlined below. Click on the the links on the left to get specific details about each plane.
747 ASB (Advanced Short Body)
Boeing announced the 747 ASB (Advanced Short Body) in 1986 as a response to the Airbus A340 and the McDonnell Douglas MD-11. This aircraft design would have combined the advanced technology used on the 747-400 with the foreshortened 747SP fuselage. The aircraft was to carry 295 passengers a range of 8,000 nmi (9,200 mi; 15,000 km).] However, airlines were not interested in the project and it was canceled in 1988 in favor of the 777.
747 CMCA - Cruise Missile Carrier Aircraft
This variant was considered by the U.S. Air Force as a Cruise Missile Carrier Aircraft during the development of the B-1 Lancer strategic bomber. It would have been equipped with 50 to 100 AGM-86 ALCM cruise missiles on rotary launchers. This plan was abandoned in favor of more conventional strategic bombers.
747 Large Cargo Freighter (LCF) Dreamlifter
Boeing Commercial Airplanes announced on October 13, 2003 that due to the length of time required by marine shipping, air transport will be the primary method of transporting parts for the 787 (then known as the 7E7). Three used passenger 747-400 aircraft were to be converted into an outsize configuration in order to ferry sub-assemblies from Japan and Italy to Charleston, South Carolina and then to Everett, Washington for final assembly. The Large Cargo Freighter has a bulging fuselage similar in concept to the Super Guppy and Airbus A300-600ST Beluga outsize cargo aircraft, which are also used for transporting wings and fuselage sections. It can hold three times the volume of a 747-400F freighter.
The LCF conversion was partially designed by Boeing's Moscow bureau and Boeing Rocketdyne with the swing tail designed in partnership with Gamesa Aeronautica of Spain. Modification is being carried out in Taiwan by Evergreen Aviation Technologies Corporation, a joint venture of Evergreen Group's EVA Air and General Electric.Boeing has already acquired the four second-hand 747-400s; one former Air China aircraft, two former China Airlines aircraft, and one former Malaysia Airlines aircraft. [Registrations N747BC (Serial 25879), N780BA (Serial 24310), N249BA (Serial 24309), and N718BA (Serial 27042).
It is much more economical for Boeing to buy used 747s and convert them than to construct these planes from scratch. The LCF is not a Boeing production model and will not be sold to any customers or see any airliner operation, and will be for Boeing's exclusive use. Another reason for modifying existing planes is the minimal regulation and flight testing required by authorities such as the Federal Aviation Administration. If the 747 LCF were produced entirely within Boeing, it would face years of development and testing in the same manner as the upcoming Boeing 747-8. Rules on airworthiness allow for the faster approval of modifications to existing aircraft that are already approved than would be the case for the approval of brand new aircraft designs.
In June 2006, the completion of the first DBL-100 cargo loader used for loading 787 parts into the 747 LCF was announced by Boeing. These loaders were designed and built by Canadian firm, TLD at its facility at Sherbrooke, Quebec and are the longest in the world at 118 foot 1 inch.
The first conversion, which drew comment because in addition to its ungainly shape, it also remained in this unpainted configuration for a long time.
In December 2006, Boeing announced the LCF would also be known as the Dreamlifter, a reference to the 787's name, the Dreamliner. It unveiled a standard livery for the aircraft that included a Dreamlifter logo reminiscent of the 787's Dreamliner logo.
The certification was to be in early 2007 however it was pushed back to June 2007. The plane had its winglets removed after excess vibration and other handling characteristics need to be dealt with prior to final certification. In the meantime as part of the flight test program, LCF delivered major sections of the 787 from partner sites around the world to the Boeing factory in Everett, WA for final assembly. The 747 LCF was granted type certification on June 2, 2007 from Federal Aviation Administration. The Dreamlifter completed 437 flight-test hours and 639 hours of ground testing since its first flight on Sept. 9, 2006.
The 747 LCF's unusual appearance has drawn comparisons to the Oscar Mayer Wienermobile and the Hughes H-4 Hercules ("Spruce Goose"). Due to its ungainly form, and exacerbated by the fact that the need for immediate testing resulted in the first model remaining unpainted for some time, Boeing Commercial Airplanes president Scott Carson jokingly apologized to Joe Sutter, designer of the 747 that he was "sorry for what we did to your plane."
Boeing plans to acquire four 747 Dreamlifters. As of June 2008, three LCFs are complete and operational, and the fourth is to become operational in 2009.
My Flickr Photos
Boeing 747 AAC (Airborne Aircraft Carrier)
In the early 1970s, the parasite fighter concept was revived, in the form of a Boeing study investigating the use of a 747 jumbo jet as flying aircraft carrier.
The study was performed under a contract from the US Air Force Flight Dynamics Laboratory (USAF FDL) at Wright-Patterson Air Force Base in Ohio.
The Boeing concept was highly ambitious, envisioning a 747-200 class jetliner as an "airborne aircraft carrier (AAC)" with a complement of ten "microfighters". The 747 would not only be able to launch and retrieve the microfighters, but also refuel them in flight or, on retrieval, load them up with fuel and weapons for a new sortie. The 747 would carry enough materiel to support three sorties per microfighter. The study also considered the use of the Lockheed C-5A cargolifter as the carrier aircraft, but not surprisingly the Boeing engineers judged the 747 the better choice.
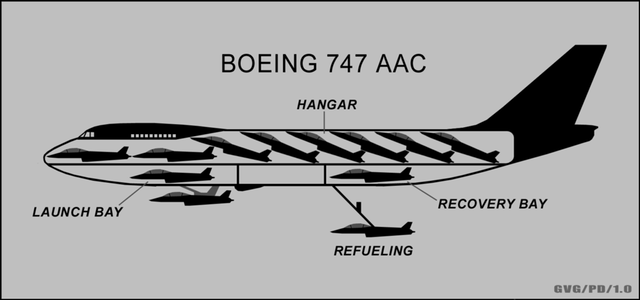
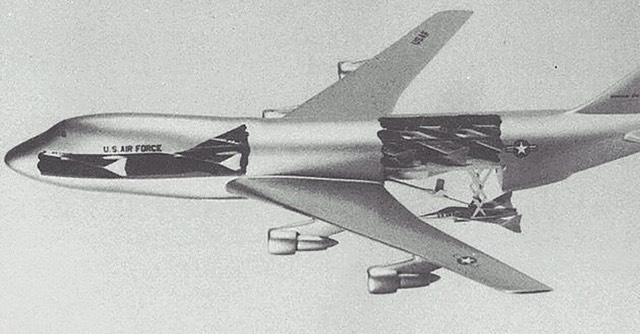
Boeing C-33
The Boeing C-33 is the US military designation for Boeing 747-400 series intended to augment the C-17 Globemaster III fleet, but the plan was cancelled in favor of purchasing additional C-17s.
Details
The C-33 designation was reserved for the Non-Developmental Airlift Aircraft project for a commercial freighter to supplement the C-17. During 1994 and 1995 the Defense Department engaged in a comprehensive process to refine airlift requirements, analyze various aspects of airlift, and prepare for an airlift fleet mix decision. A Defense Acqusition Board review satisfied congressional direction to conduct a Cost And Operational Effectiveness Analysis, to consider the C-17 and mixes of alternative aircraft, and to preserve intertheater airlift capacity. Initial material solutions considered included: buy a modified Boeing 747-400 NDAA, restart the C-5 production line, extend the C- 141 service life, and continue C- 17 production. The field eventually narrowed to: the Boeing 747-400, the Lockheed-Martin C-5D, and the McDonnell Douglas C- 17.
The NDAA study [The NDAA Report: An Application of Commercial Acquisition (Washington, D.C.: Non-Developmental Airlift Aircraft System Program Office, 1994)] focused on a minimally modified Boeing 747 cargo air-craft. These “minimal” modifications included hardened decks and a flip-up nose and ramp system for ease of straight-in loading versus the side-mounted-cargo-door style loading of the commercial industry. Consequently, the price for the NDAA alternative increased from under $150 to about $200 million per aircraft.41 Nevertheless, after examining several options, the most cost-effective solution was an 86/30 mix of C-17 and NDAA aircraft.42 This mix, however, did not allow for a full strategic brigade airdrop nor was it optimized for tactical airlift requirements and lesser regional contingencies in support of peace enforcement scenarios.
Boeing E-4 Advanced Airborne Command Post
The Boeing E-4 Advanced Airborne Command Post, with a project name of "Nightwatch", is an aircraft operated by the United States Air Force (USAF) and is specially built to serve as a survivable mobile command post for the National Command Authority, including the President of the United States, the Secretary of Defense, and successors. The E-4s are operated by the 1st Airborne Command and Control Squadron in the 55th Wing out of Offutt Air Force Base, Nebraska.
Two of the original 747-200 airframes were originally planned to be commercial airliners. When the airline did not complete the order, Boeing offered the airframes to the USAF as part of a package leading to a replacement aircraft for the then used NEACP EC-135J model. Under the 481B NEACP (National Emergency Airborne Command Post) program the Air Force Electronic Systems Division awarded Boeing a contract in February 1973 for two unequipped aircraft, E-4A and powered by four JT9D engines, to which a third aircraft was added in July 1973. The first E-4A was completed at the Boeing plant outside Seattle, Washington in 1973. E-Systems won the contract to install interim equipment in these three aircraft, and the first completed E-4A was delivered to Andrews AFB, Maryland in December 1974. The next two were delivered in 1975, the third differed by being powered by the GE F103 engine, which was later made standard and retrofitted to the previous two aircraft. The "A" model effectively housed the same equipment as the EC-135, but offered more space and an ability to remain aloft longer than an EC-135.
Additionally the E-4 was capable of operating the "Looking Glass" mission of the Strategic Air Command (SAC). The E-4A aircraft were capable of remotely launching retaliatory strikes from SAC missile fields. SAC subsequently relinquished the aircraft to full time use by the Office of the Joint Chiefs of Staff.
In December 1973 a fourth aircraft was contracted for, which was fitted with more advanced equipment, resulting in the designation E-4B. On 21 December 1979 Boeing delivered the first E-4B (AF Serial Number 75-0125), which was distinguished from the earlier version by the presence of a large "hump" on the dorsal surface directly behind the upper deck. This contains the aircraft's SHF satellite antenna.[4] By January 1985 all three E-4As had been retrofitted to E-4B models. The E-4B offered a vast increase in communications capability over the previous model and was considered to be 'hardened' against the effects of electromagnetic pulse (EMP) from a nuclear blast. Hardening the aircraft meant that all equipment and wiring on board was shielded from EMP. Additional steps were taken to block radiation from the aircraft's cabin air management system and cockpit, including the novel use of the same screens used to cover the windows of microwave ovens placed over the cockpit windows.
Estimates at the time of the production of the first E-4B placed the developmental cost at nearly US$ 1 billion. The roll out cost of the fleet was placed at approximately US$ 250 million each. The E-4B is capable of operating with a crew of 48 to 112 people, the largest crew of any aircraft in US Air Force history.
In 2005 the Air Force Appropriations Committee awarded Boeing a US$ 2 billion contract for the "continued upgrade" of the E-4B fleet, a considerable amount of money considering that there are only four aircraft. This contracted work is expected to take five years to complete.
Boeing KC-33A
A proposed 747 was also adapted as an aerial refueling tanker and was bid against the DC-10-30 during the 1970s Advanced Cargo Transport Aircraft (ACTA) program that produced the KC-10A Extender.
This aircraft is based upon existing Boeing 747 aircraft and combines midair refueling capabilities with a reinforced upper deck that can carry vehicles, particularly light armor, such as the M113A3. A fold-out ramp would be carried in the nose of the aircraft to allow vehicles to drive on and off of the aircraft. Under the deck would be a set of tanks and pumps to allow the aircraft to refuel other aircraft or simply engage in very long-range missions.
Boeing VC25 Air Force One
Air Force One Photos
The mission of the VC-25A aircraft -- Air Force One -- is to provide air transport for the president of the United States. The presidential air transport fleet consists of two specially configured Boeing 747-200B's -- tail numbers 28000 and 29000 -- with the Air Force designation VC-25A. When the president is aboard either aircraft, or any Air Force aircraft, the radio call sign is "Air Force One".
Principal differences between the VC-25A and the standard Boeing 747, other than the number of passengers carried, are the electronic and communications equipment aboard Air Force One, its interior configuration and furnishings, self-contained baggage loader, front and aft air-stairs, and the capability for inflight refueling. The VC-25A is capable of flying half way around the world without refueling and can accommodate more than 70 passengers.
Accommodations for the president include an executive suite consisting of a stateroom (with dressing room, lavatory and shower) and the president's office. A conference/dining room is also available for the president, his family and staff. Other separate accommodations are provided for guests, senior staff, Secret Service and security personnel, and the news media. Two galleys provide up to 100 meals at one sitting. Six passenger lavatories, including disabled access facilities, are provided as well as a rest area and mini-galley for the aircrew. The VC-25A also has a compartment outfitted with medical equipment and supplies for minor medical emergencies.
The first VC-25A -- tail number 28000 -- flew as "Air Force One" on Sept. 6, 1990, when it transported President George Bush to Kansas, Florida and back to Washington, D.C. A second VC-25A, tail number 29000 transported President Bill Clinton and former Presidents Carter and Bush to Israel for the funeral of Prime Minister Yitzhak Rabin. The VC-25A will usher presidential travel into the 21st century, upholding the proud tradition and distinction of being known as "Air Force One".
VC-25 aircraft are extensively modified B-747-200s with the basic airframe technology of the 1960s. The aircraft incorporates state-of-the-art avionics and communications equipment with Stage III compliant engines. Boeing is currently delivering B-747s throughout the world, so the logistics support base appears secure for the foreseeable future. With the continuing march of technology and the prestige attached to the U.S. Presidential airlift fleet, Air Force plans recommend a system review date of 2010. At this point, the aircraft will have been in service 20 years, and commercial operators will have retired their B-747-200s counterparts from front-line service.
These aircraft are flown by the presidential aircrew, maintained by the Presidential Maintenance Branch, and are assigned to Air Mobility Command's 89th Airlift Wing, Andrews Air Force Base, MD.
Air Force One is managed by Tinker Air Force Base personnel from the Contractor Logistics Support Management Directorate. Tinker has managed Air Force One since the airplanes were originally delivered back in 1990. The directorate manages Air Force One's day-to-day issues like supply and logistics support, while at the same time ensuring the aircraft are maintained to Federal Aviation Administration regulatory standards. This support also includes engineering and technical support, production management, modification management, budget management and contracting. Programmed Depot Maintenance [PDM] is also managed by this directorate, but the work is contracted out to Boeing's Wichita, Kan., facility. PDM is performed on one of the two Air Force One aircraft every year. To comply with a recent FAA mandate, one aircraft was updated with a new Fuel Quantity Indicating System.
Heavy maintenance, completed on that aircraft in December 2000, included installation of the Global Positioning System and Flight Management Computer System. These systems were added as part of increasing FAA mandates to help make the aircraft more efficient. The second Air Force One aircraft was compliant with the FAA mandate when it rolled out of PDM later in 2001. In the wake of the TWA Flight 800 explosion, the FAA and the National Transportation Safety Board issued an Airworthiness Directive requiring anyone who maintains a 747 install a new FQIS with safety provisions that resulted from the TWA 800 investigation.
In the early 1990s Air Force One was secretly outfitted with a directed infrared countermeasures (DIRCM) system to protect it from a missile attack. According to some reports, the plane can also eject flares to throw heat-seeking missiles off course.
Evergreen Supertanker
The Evergreen Supertanker is a Boeing 747-200, modified by Evergreen International Aviation into a 24,000 US gallon (94,850 litre) capacity aerial firefighting aircraft. This is double the capacity of the next largest air tanker in operation, the Tanker 910. The Evergreen Supertanker was scheduled to be available to fight fires from summer 2008 but has not yet entered service.
Unique technology is used on the Evergreen Supertanker in order to allow an aircraft as large as a 747 to carry out aerial fire fighting.
Current fire fighting aircraft use a gravity drop system. Doors in the underside of the aircraft open, allowing the contents of the tanks to discharge. This type of system requires an aircraft to fly very low, typically 200ft above ground level. The Evergreen Supertanker has a pressurised system. This can disperse retardant under high pressure, for an overwhelming response, or drop retardant equivalent to the speed of falling rain. This system allows the aircraft to operate within its design criteria.
Using the pressurised system, the aircraft can deliver retardant to the scene of a fire whilst flying at a height of 400 to 800ft, at approximately 140kts (160mph) (260kph), configured as if it were on approach for landing.
The Evergreen Supertanker’s tank system can be configured for segmented drops, allowing the contents of the tank to be released at multiple intervals while in flight.
Shuttle Carrier Aircraft
NASA uses two modified Boeing 747 jetliners, originally manufactured for commercial use, as Shuttle Carrier Aircraft (SCA). One is a 747-100 model (NASA 905), while the other is a short range 747-100SR (NASA 911). The two aircraft are identical in appearance and performance.
The 747 series of aircraft are four-engine intercontinental-range, swept-wing "jumbo jets" that entered commercial service in 1969. The two SCAs are under the operational control of NASA's Johnson Space Center, Houston, TX.
The SCAs are used to ferry Space Shuttle orbiters from landing sites back to the Kennedy Space Center launch complex in Florida and also to and from other locations too distant for the orbiters to be delivered by ground transportation.
An orbiter is placed atop the SCA by a Mate-Demate Device (MDD), a large gantry-like structure that hoists the orbiter off the ground for post-flight servicing, and then mates it with the SCA for ferry flights.
Features which distinguish the two SCAs from standard 747 jetliners are:
- Three struts, with associated interior structural strengthening, protrude from the top of
the fuselage (one forward, two aft) on which the orbiter is attached
- Two additional vertical stabilizers, one on each end of the standard horizontal stabilizer,
to enhance directional stability
- Removal of all interior furnishings and equipment aft of the forward cabin doors
- Instrumentation used by SCA flight crews and engineers to monitor orbiter electrical loads during the ferry flights and also during pre- and post-ferry flight operations
NASA 905
NASA 905 was obtained from American Airlines in 1974 and became the first SCA. Shortly after it was accepted by NASA it was flown in a series of wake vortex research flights at the Dryden Flight Research Center in a study to seek ways of reducing turbulence produced by large aircraft. Pilots flying as much as several miles behind large aircraft have encountered wake turbulence that have caused control problems. The NASA study helped the Federal Aviation Administration (FAA) modify flight procedures for commercial aircraft during airport approaches and departures.
Following the wake vortex studies, NASA 905 was modified by Boeing to its present SCA configuration and the aircraft was returned to Dryden for its role in the 1977 Space Shuttle Approach and Landing Tests (ALT). This series of eight captive and five free flights with the orbiter prototype Enterprise, in addition to ground taxi tests, validated the aircraft's performance as an SCA, in addition to verifying the glide and landing characteristics of the orbiter configuration paving the way for orbital flights.
NASA 911
NASA 911 entered service with as an SCA in November 1990. It was obtained from Japan Airlines (JAL) in 1989 and modified by Boeing.
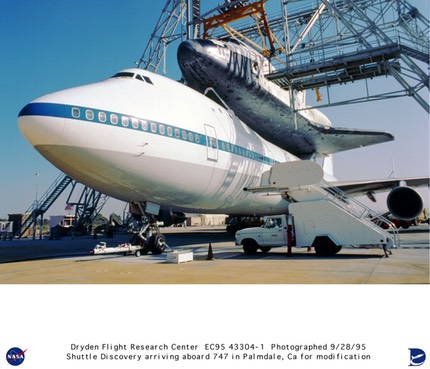
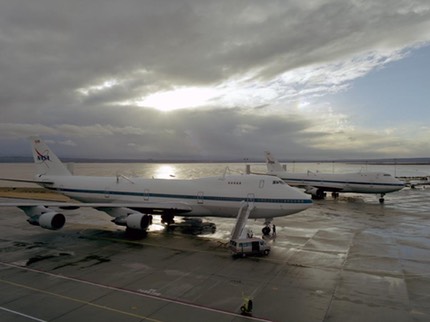
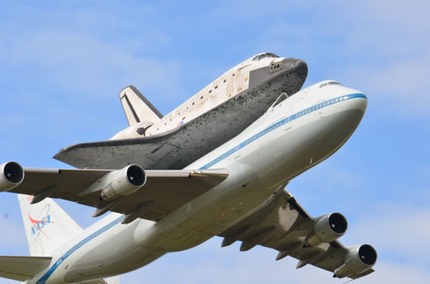
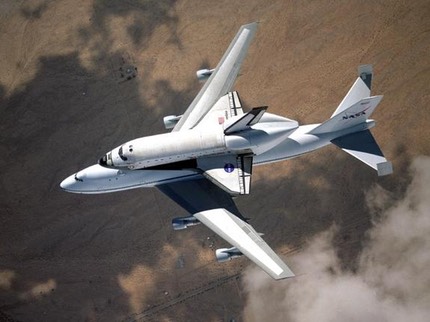
Images courtesy of NASA
SOPHIA - Stratospheric Observatory for Infrared Astronomy
The Stratospheric Observatory for Infrared Astronomy (SOFIA) is a joint project of NASA and the German Aerospace Center (DLR). Universities Space Research Association (USRA) was awarded the prime contract by NASA in 1996 for development, operation of the observatory and management of the American part while the DSI (Deutsches SOFIA Institut) manages the German part (mainly science and telescope related).
SOFIA is based on a Boeing 747SP wide-body aircraft. The aircraft has been modified to carry a 2.5 meter diameter reflecting telescope in the aft section of the fuselage. This telescope is designed for infrared astronomy observations at altitudes of about 41,000 feet (about 12 km) in the stratosphere. The water vapor in the Earth's atmosphere blocks some infrared wavelengths from reaching the ground, but SOFIA's flight capability allows it to rise above almost all of the water vapor in the Earth's atmosphere. At the aircraft's cruising altitude, 85% of the full infrared range will be available. The aircraft can also travel to almost any point on the Earth's surface, allowing observation from the northern and southern hemispheres.
Once ready for use, the expectation is for observing flights to be flown 3 or 4 nights a week for the next 20 years. SOFIA is now based at NASA's Dryden Aircraft Operations Facility at LA/Palmdale Regional Airport, California, while staff at NASA Ames Research Center, in Mountain View, California, operate the SOFIA Science Center where astronomical observation missions are planned for the flying observatory.
In mid-2009, the aircraft will undergo flight tests at high altitude cruising speed with the telescope door open. This test phase is scheduled to run through the end of 2009, after which SOFIA will begin limited science observation flights. Normal science observation flights should begin in 2011 and the observatory is slated for full capability by 2014.
YAL-1 Airborne Laser
The Boeing YAL-1 Airborne Laser (ABL) weapons system is a megawatt-class chemical oxygen iodine laser (COIL) mounted inside a modified Boeing 747-400F. It is primarily designed as a missile defense system to destroy tactical ballistic missiles (TBMs), similar to the Scud, while in boost phase.